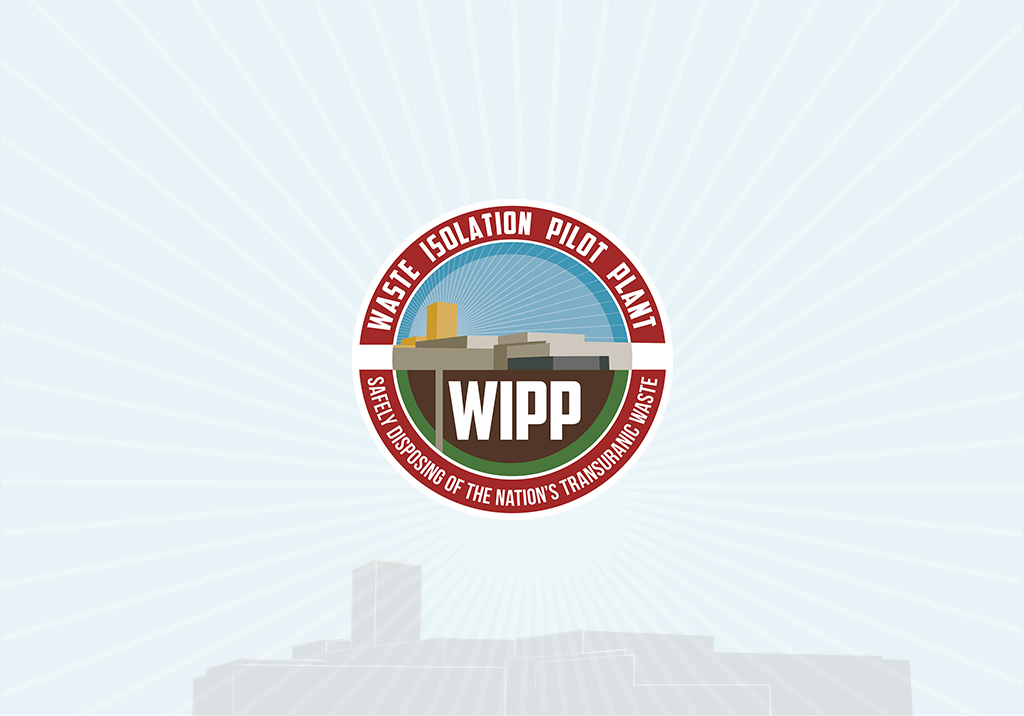
Way cleared for emplacement in final Panel 7 room
March 10, 2022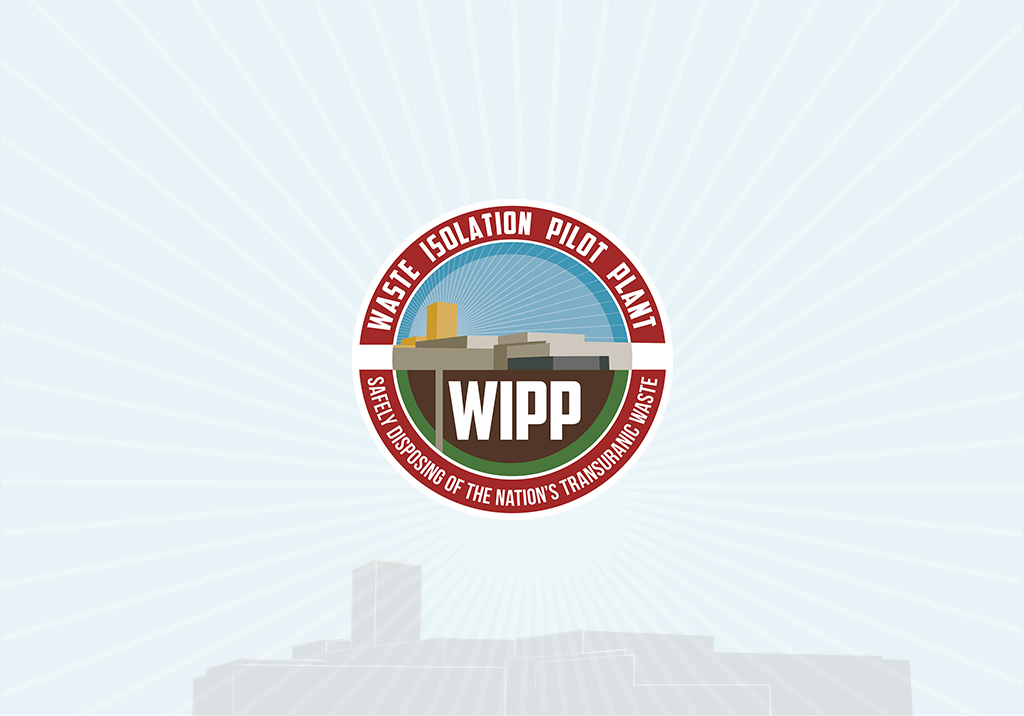
Department of Energy Office of Environmental Management Visits WIPP
February 23, 2022Down & Up
There’s something big going down at WIPP. A 101,000-pound work platform known as a Galloway was lowered into the new utility shaft in January to begin the next phase of construction on what will eventually be a 2,275-foot deep airway into the mine. The utility shaft, at 26 feet in diameter, will be the largest of WIPP’s five shafts.

Operations known as a “pre-sink” excavated the shaft down to 116 feet, setting up the next step. The Galloway, a four-story tall cylindrical work platform named for a Scottish mining engineer, will be key to blasting and excavation operations in the months ahead. When mining has reached the 2,150-foot level, a mining machine will begin carving out passageways, or drifts, eastward, toward the existing WIPP facility.

With the Galloway placed in the shaft, a metal frame, known as a headframe, is being constructed. Cables from winches will run over pulleys, known as bull wheels, atop the headframe and connect to the top of the Galloway. Lift buckets connected to other winches will come up through the middle of the Galloway, filled with rubble blasted loose at the bottom of the shaft.
When the shaft is completed, two large fans will push air down the shaft into the underground as part of a drastic improvement of WIPP’s ventilation system. WIPP’s 11th and 12th panels are planned for the west side of the current underground, in the direction of the utility shaft. Five drifts, two mined by the shaft contractor and three that will be mined by WIPP crews, will connect the existing mine to the utility shaft area.

WIPP crews have started the first drift at South 850, heading west to West 620. Drift cuts at South 700 and South 1000 will connect to West 620. A side cut will connect to the current air intake shaft, which is being converted for use as an exhaust shaft for mining.
On the other side of the WIPP site, the under-construction Safety Significant Confinement Ventilation System (SSCVS) will use six 1,000-horsepower fans to pull air through the mine in filtered or unfiltered modes. The 540,000 cubic feet per minute of airflow will be a 217% increase over the current system’s 170,000 cfm, allowing for simultaneous waste emplacement, mining and bolting.
The Industrial Company (TIC), a subsidiary of Kiewit, has completed the enclosure of the 25,000 square-foot Salt Reduction Building (SRB) with concrete walls and roof, with interior painting underway under temporary lighting provided from the nearby Xcel substation. Concrete masonry walls are under construction within the SRB.

The SRB will act as a prefilter, using de-dusters and water misters to drop salt out of the air pulled from the underground before it heads to the 50,000 square foot New Filter Building (NFB). In the NFB, air will flow through switchable high-efficiency particulate air (HEPA) filter banks before exhausting out a 125-foot-high exhaust stack.
The NFB’s foundation, known as slab-ongrade, was completed weeks early and that has allowed visible progress on the building. Concrete placements continue on the building’s walls, using a 200-ton crane, with the focus starting to shift to the roof decking over the air intake area, known as a plenum.
“Our subcontractor is making great progress on the new permanent ventilation system,” said DOE Carlsbad Field Office Manager Reinhard Knerr. “Anyone driving by the WIPP site can see how the skyline is changing in a positive way that will support future WIPP operations.”