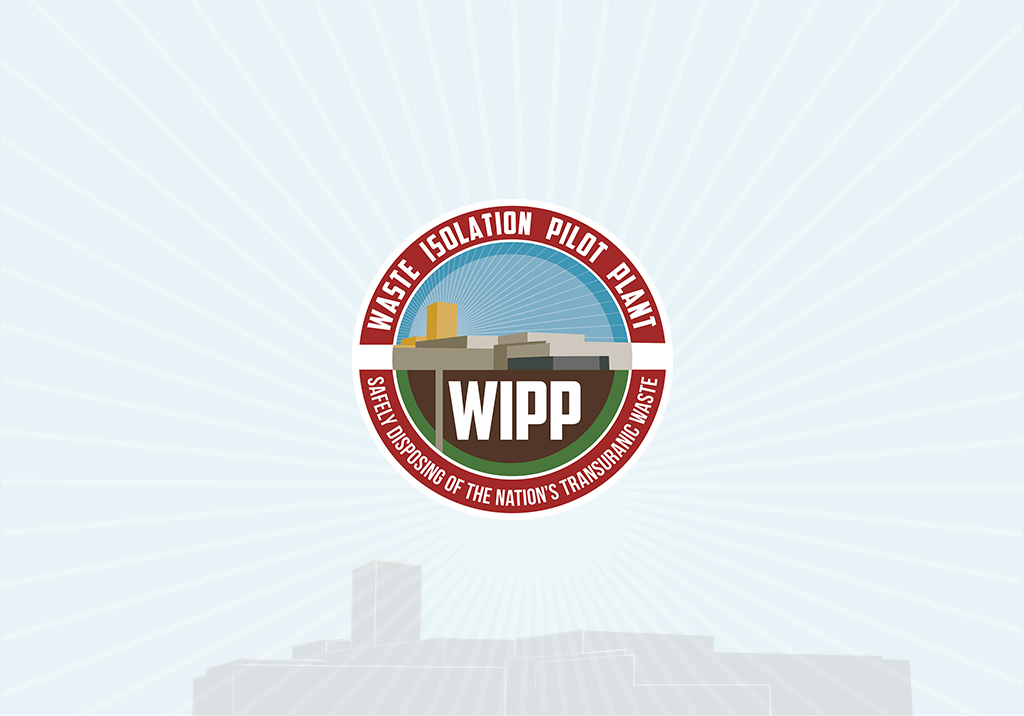
WIPP Mine Rescue Teams Finish in Top 15 at National Competition
September 2, 2022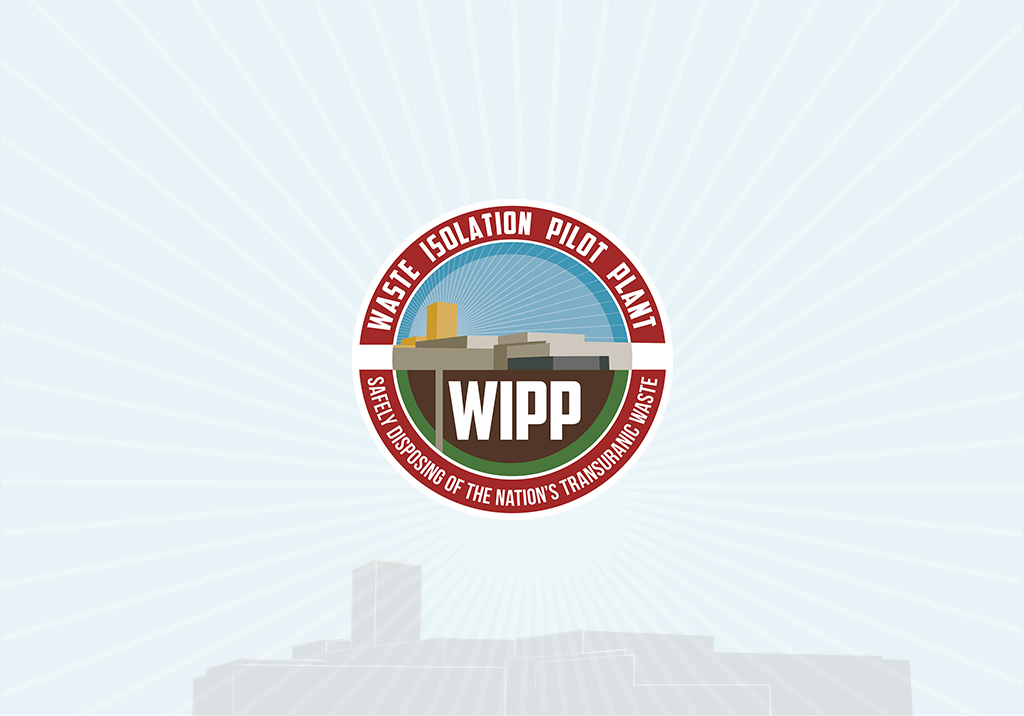
WIPP Community Days Provide Opportunity for Learning and Exploration
August 2, 2022WIPP’s Big Dig to Lead to New Utility Shaft as Crews Advance Massive Ventilation System
CARLSBAD, N.M. – Blast. Dig. Hoist. Dump.
That’s the basic but effective method being used at EM’s Waste Isolation Pilot Plant’s (WIPP) utility shaft excavation, where resumption of operations more than two years after the start of COVID-19 has crews on their way deep into the desert salt.
The new shaft and a permanent ventilation system known as the Safety Significant Confinement Ventilation System (SSCVS) are part of a multimillion-dollar investment in upgrading WIPP’s infrastructure so the facility can operate safely and compliantly for decades to come.

“It’s exciting to see the process get underway,” said Sean Dunagan, president and project manager for Nuclear Waste Partnership (NWP), WIPP’s management and operations contractor. “The crews are making great progress, and doing it safely and compliantly.”
Crews from South Africa’s Shaft Sinkers and Colorado’s Harrison-Western have reached 181 feet toward an eventual goal of 2,275 feet for the shaft. It is WIPP’s fifth utility shaft, and upon completion, it’ll be the site’s largest at 26 feet in finished diameter.
The shaft will be an air intake for the massive SSCVS being constructed on the other side of the WIPP site, 26 miles east of Carlsbad. When finished, it will increase airflow to the WIPP underground from the current 170,000 cubic feet per minute (cfm) of filtered ventilation to as much as 540,000 cfm, an increase of 217%.

A so-called “pre-sink” operation excavated the utility shaft to 116 feet and installed an angled air intake shaft where surface-mounted fans will push air down the shaft and into the underground.
The blasting and excavation occurs around the clock. Workers drill holes and set explosive charges in half of the shaft circle. Rubble from the subsequent explosion is scooped by remote-controlled mechanical arms on the bottom of a cylindrical four-level work platform known as the Galloway that is lowered into the shaft. The mechanical arms dump debris into a pair of buckets that are pulled up through two holes in the Galloway to the surface. The debris is dumped into chutes and onto a concrete pad where a front-end loader scoops it into a waiting truck to be hauled away.
Then the process is repeated on the other half of the circle.
While one operator works the excavation arms, workers on other levels are lining the shaft with concrete.
The two buildings of the SSCVS project, the Salt Reduction Building (SRB) and New Filter Building (NFB), are marking rapid progress.
The Industrial Company (TIC), a subcontractor to NWP, has successfully poured 38 of the 44 concrete walls of the NFB’s plenum, a giant holding area where air coming from the SRB collects before being pulled through high-efficiency particulate air (HEPA) filtration by the NFB’s 1,000-horsepower fans. The building contains six of the fans; four will operate at a time with one in reserve and one rotated out for maintenance.
Four of the NFB exhaust fan assemblies have been delivered to the site and stored in the SSCVS fabrication building.
At the NFB, TIC crews also have poured eight of 13 elevated concrete decks, all 117 concrete walls and installed all precast interior columns.

All six of the SRB’s filter units have been delivered and installed, allowing the building to be enclosed with its final precast wall panels. The SRB will prefilter the air headed to the NFB. Air coming to the surface through the exhaust shaft is heavily laden with salt, which will first enter the SRB through 14-foot ductwork into filter units. The units drop salt out of the airflow through the use of filters and misters. The salt brine from the misters will flow into brine tanks and then a brine collection pond. Prefiltered air is then pulled via turbo fans near the ceiling of the building and driven toward the NFB.
Once pulled through the HEPA filters in the NFB, air will be exhausted through a 125-foot-high stack.